en lui retirant des
substances inutiles pour la qualité d'un acier choisie.
-Sur photo, le coke est vidé dans un wagon pour aller se refroidir.
Cest le panacche de vapeur blanche, que l'on aperçois de loin!
-Le coke est du carbone, presque pur,
d'une structure résistante à l'écrasement. On extrait son goudron par condensation, de
l'ammoniac par sulfatation, du benzol par lavage et du gaz comme du méthane ou de l'hydrogène. Sur une tonne de charbon on obtient 750kg de coke, 35kg de
goudron, 10kg de sulfate d'ammoniaque, 7kg de benzol, 350m3 de gaz. A la sortie du four le coke sera transportée vers l'agglomération.
- le coke sert de combustible aux hauts-fourneaux
pour faire fondre le minerai. Pour cela, on ne peut pas utiliser le charbon directement car il faut le débarrasser de toutes ses impuretés (qui se
mélangeraient à la fonte) et de son humidité. On doit, alors, distiller le
charbon. dans des fours pour en extraire les matières volatiles. Le coke est alors obtenu par pyrolyse du coke
- Au cours de la cuisson du
charbon pendant 18 à 40 heures à l'abri de l'air, dans des fours à 1 100 °C. Comme il n’y a pas d’oxygène dans ces fours, le charbon ne brûle pas. Une fois
le charbon dans la batterie de la cokerie à une température de 100 à 200°C il va sécher, toute l'eau qu'il contient va s'évaporer. Jusqu'à 350° la pâte
entre en fusion, il se ramollit (dégage du goudron) puis vers 500°C et plus il se solidifie (dégagement d'hydrogène) c'est la phase de semi carbonisation.
celui-ci se débarrasse d'un certain nombre de polluants comme les goudrons, le benzol, le sulfure d'hydrogène.
-A la fin de la cuisson, le saumon de coke est refroidi
brutalement par aspersion de 20 m3 d'eau, c'est là que l'on voit le grand
panache de fumée et vapeur blanche au dessus de la cokerie, puis le coke est dirigé vers l'atelier de criblage pour être broyé et mélangé au minerai.
- Un haut fourneau accomplit cinq
opérations:
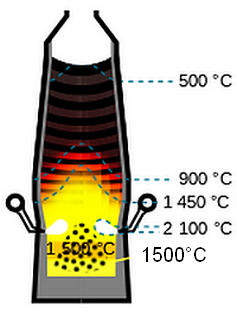
Désoxyder le minerai de fer.
• Faire fondre les scories.
• Faire fondre le fer.
• Carburer le fer.
• Séparer le fer des scories.
-
Le tout produit de La fonte liquide.
-Cette fonte étant très cassante
est non laminable, ni emboutissable. On peut en trouver sur les
routes "Les plaques dégouts".* (elle est cassante!) -Avec des hauts fourneaux qui vont atteindre jusqu'à 80 m de haut,
5.000 mètres cube, des températures de 1.600 degrés et des productions en continu jusqu'à 10.000 tonnes.
-Le minerai de fer et le coke ainsi
préparés sont enfournés au haut fourneau par bandes transporteuses en alternance,
coke métallurgique et minerai entrent par le haut du haut fourneau et par le poids et la fonte descendent progressivement à la
base du haut fourneau, le coke en présence d'air se transformant en monoxyde de carbone, produisant ainsi une quantité de chaleur suffisante pour faire fondre le minerai, la gangue et le fondant.
Ce monoxyde ayant alors un mouvement ascendant, va au contact du minerai réduire les oxydes de fer.
De leur coté, gangue et fondant se combinent pour former un produit relativement fusible et beaucoup moins dense que la fonte. Ce liquide
surnage au-dessus de la fonte liquide de laquelle on le sépare par décantation. On dit du Laitier!
-Le laitier :correspond à la gangue du minerai à laquelle s'ajoutent les
cendres du coke, Sa composition est étudiée pour assurer une vidange facile du creuset, mais aussi désulfurer la fonte, voire
protéger le creuset. Après la coulée, selon son conditionnement, il devient une
matière première, appréciée. Il est essentiellement utilisé dans la fabrication de ciment (2/3 de la production en Europe, pour essentiellement le laitier
vitrifié) ou comme remblais routier (1/3 de la production en Europe, essentiellement du laitier cristallisé) . On l'utilise aussi, entre autres, dans
la fabrication du verre, de la laine de roche ou comme granulat de béton.
-La fonte (alliage de fer et de carbone
est obtenue à la base du haut fourneau: elle est recueillie dans des creusets puis acheminée par la suite vers l'aciérie tandis que les sous-produits (gaz de haut fourneau,
Laitier et chaleur sont récupérés et valorisés.
-La fonte liquide part à l'aciérie ici, la base des hauts fourneaux
avec une coulée. dans des wagons spéciaux appelés " poches- tonneaux" sortes d'énormes bouteilles thermos en forme de cigare capables de maintenir la
fonte à température (1500°) pendant plus de 48 heures. C'est à l'aciérie que l'on va transformer cette fonte en acier.
- Convertisseur Aciérie -
Il converti la fonte en acier. L’étape initiale de production de l’acier consiste à
extraire les impuretés et le carbone (pas tout) présents dans le fer. Les éléments d’alliage sont ajoutés en quantités précises pour donner aux aciers
alliés des caractéristiques particulières.
.ici au dessous, unepoche se vide dans un convertisseur.
-Photo convertisseur (musé) ici on peut remarquer sa taille!
-La fonte liquide est mélangée dans un
convertisseur avec de l'acier usagé. (des chutes de métal, de la
récupération diverses.) Le rôle essentiel du convertisseur est de brûler le
carbone de la fonte pour arriver à un acier liquide et, une série de réactions chimiques se
déroulent successivement dans ce réacteur :
On procède alors à l'affinage de la
fonte pour obtenir de l'acier relativement pur. Pour cela il faut éliminer :
- une partie du carbone
- une partie du manganèse
- la quasi totalité du phosphore
- la quasi totalité du silicium .
-On procède par oxydation de ces
éléments, les oxydes se séparant plus facilement du mélange, soit parce qu'ils sont gazeux, soit parce qu'ils se combinent aux autres oxydes ou à un additif tel que la chaux vive, pour former des scories de faible densité qui restent à la
surface.
-Cette opération appelée conversion se fait par insufflation d'oxygène
par le fond du convertisseur. En fin de purification, on rajoute des alliages fer-manganèse pour réduire l'oxyde de fer formé lors de la conversion.
Voila, nous avons de l'acier, reste à letransformer en Brames pour
arriver à en faire des
bobines de métal.
-Ici a droite des Lingotières: Ce sont des moules Lingotières verticales! -Le métal liquide (pouvait être coulé dans une lingotière verticale) .Cela
ne se fait plus
- Maintenant, il part en poche vers une ligne de coulées en continue
-En coulée continue -----------------------------
La solution consiste alors à couler le métal dans un moule
refroidi, et une lingotière, dont le fond est fermé par le métal (lui même) solidifié. La lente extraction de ce métal est
compensée de manière continue par le remplissage du moule. (moule variable (MALV)
- La poche de métal liquide venant des convertisseurs
est verséé dans une poche qui se trouve sur un tourniquet qui possède 2 poches. une qui se vide et l'autre qui prendra la relève .
- Une poche se
vide dans un répartiteur quien
se vidant va rempli une lingotière " Moule variable..."MALV"
(sur schéma), Il s'agit alors de solidifier l'acier sous forme d'une longue bande ininterrompue qui sera découpée par des
chalumeaux de façon à donner des brames. Une brame est un parallélépipède d'acier d'environ 11 m90 de long sur
1,900 m de large sur 35 cm d'épaisseur. Elle pèse en moyenne 25 tonnes et seralaminée pour devenir une bobine.
-
Le métal refroidit, et poussé par le poids du métal
liquide il descend, guidé par des glissières et des rouleaux.
le métal est assez refroidi pour tenir seul sa forme. Il arrive à la fin de sa descente verticale il est dans la courbe de descente
image à gauche et à droite , on voit que le métal est assez solidifié pour être coupé à a
la longueur voulue par la station d'oxycoupage (2 chalumeaux ici.)
La partie coupée devient une Brame.
-Puis la Brame est stockée, avant de partir pour un four, poussant, qui va la réchauffer
afin de pouvoir la laminer en bobine. Sur le train à bande (Laminoir de 7 cages) ou vendue directement au client au format demandé par ce client.
-Avant de laminer les brames, elles doivent être chauffées à une
température allant de
1000°C à 1270° .Cette opération est effectuée dans les fours poussant du laminoir à chaud (Poussant ) car, Une brame
qui entre a l'autre bout du four pousse toutes celles qui sont devant elle est fait tomber
(au moment voulu) la brame qui est prés de la sortie. Va, directement au laminage a chaud.
- Le laminage à chaud - -----------------------------
-La brame à la sortie du four est couvert d’une couche d’oxyde.
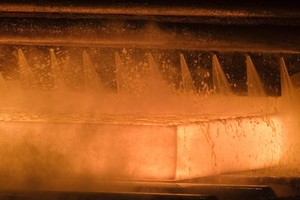
-L'oxyde ne s'allonge pas il se décolle de la brame, mais reste dessus
et doit être
éliminée avant d’être enroulée. La couche est alors, brisée et enlevée par un jet d’eau ayant une pression de 120 bars .(image
de droite ici au dessus . Ensuite, la brame est amincie en plusieurs étapes, puis. dirigée au laminoir à 7 cages consécutives.
1 -Sortie du four - 2-et 3 Décalaminage - 4-laminage cours -
-Chaque cage de laminage va réduire l’épaisseur et allonger la tôle . A la sortie de ligne, l’épaisseur, la largeur, le profil, la planéité et la température de
la tôle sont contrôlés.
-La brame a fait plusieurs passes, dans un dégrossisseur réversible ou un dégrossisseur continu qui réduit son épaisseur
pour atteindre approximativement entre (exemple) 6 et 3 cm. L’épaisseur finale sera atteinte dans un train finisseur .
(laminoire à froid) Voir plus bas
-- Après laminage à chaud. -----------------------
Les coils partent par wagon,(
exemple de
Dunkerque) pour aller (exemple. Mardyck). Ils sont stockés soit dehors soit en halle. parfois encore très chaud. La
rouille s'installe vite. Il faut alors, les décaper avant de passer dans un laminoir à froid pour être transformés en bobines (exemple) de 3 à 0,25 mm d'épaisseur.
- Décapage -__________________________
-Ces Coils doivent être débarrassés de leur
oxydation, (rouille) pour ne pas s'incruster dans les cylindres des laminoirs,
créant ainsi des défauts d'aspect et de qualité métal . (Pailles)
-Le décapage : sert à enlever l'oxyde (rouille) afin d'éviter les incrustations d'oxyde dans le métal lors du laminage à froid.
en même temps il y a une inspection visuelle pour défauts de surface et contrôle l'épaisseur, largeur car souvent dérivée par 2 cisailles de rives
(après soudeuse) . Tout ce fait en continu, les coils sont
soudés bout à bout à l'entrée de la ligne. En sortie ligne, la bande peut aller se faire laminer en continu. ou sortir en bobines. A droite
la soudeuse qui soude les coils bout à bout pour décapage en continue. La bobine partira, ensuite au laminage à froid.-Le décapage, se fait en
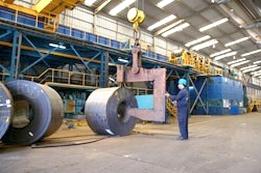
faisant défiler la bande de métal dans
un bain d'acide chlorhydrique chaud. Le bain d'acide chlorhydrique se situe en hauteur, la bande et en même temps contrôlée,en épaisseur et aussi visuellement,
pour éviter des défauts de surface, pouvant abimer les cylindres du laminage
.-Dessous les bains il y a plusieurs étages de rouleaux tendeurs qui permettent de
conserver une longueur de tôle importante , pour nepas
arrêter la bande de défiler dans les bains lors d'un arrêt a l'entrée de la
ligne pour souder les colis bout a bout. ou aussi permettre de sortir les bobines en fin de ligne, sans arrêter la ligne décapage.
Voir ci-dessous (accumulateur - le déroulement en continu de la bande.)
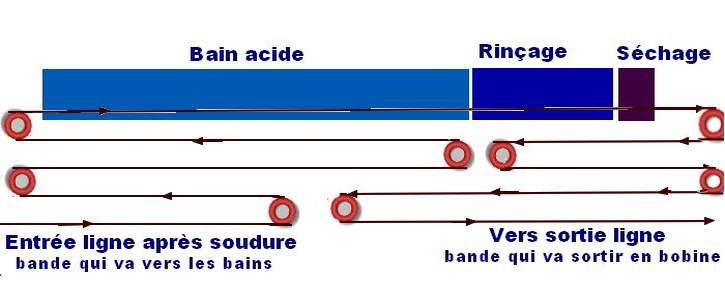
-Principe de l'Accumulateur (de longueur).
A gauche, A l'entrée de la ligne de décapage, un coil se déroule pour être soudé
(bout à bout) a la fin d'un coil qui vient de finir de se dérouler et qui passe dans le bain d'acide.
-Le décapage peut être aussi en continu avec le tandem 5 cages (Laminoir à froid)
Il se trouve alors, une toure d'accumulation de longueur si une ligne arrête (un moment) l'autre continue tant qu'il restera de la longueur de bande dans les tours
- Le Laminage à froid -------Mise a épaisseur
client---------------------
Ici, ce laminoir a 5 cages et 20 cylindres, 4 par
cage): Le principe :Diminution de l'épaisseur par étirement en passant entre les
cylindres des 5 cages.
-Laminage en cours - On voit des cylindres neufs qui attendent de
remplacer les cylindres qui seraient usés ou marqués par un défaut.
-On peut voir les cylindres.
(un gros cylindre d'appui et dessous, 2 plus petits,entre les quelles passe la bande et dessous, encore un gros cylindre d'appui) qui empêche aussi aux cylindres de dessus de se déformer.
Le tandem : laminoir : constitué de plusieurs cages, l'une après l'autre (d'un
nombre fluctuant entre 4 et 6 (ici 5,) la bande passe simultanément dans les cages.
-La bande (exemple) d'une épaisseur de 6 mm en entrée
du laminoir aura 1,5 mm en sortie; CE sera appellé
Exemple:( Tôle mince pour
Voitures )
-Ou, 3mm en entrée et 1,5mm en et 0,15 en sortie,
Ce sera appelé Fer blanc(expl) pour boite alimentaire ou autres. La bande se déroule et passe entre les cylindres des 5 cages. et s'enroule en sortie
avec une épaisseur voulue. Il y a, la tôle très fine 0,50 à 0,15 pour faire (exemple) boites de conserves. ou Tôle mince 0,70 mm pour faire (exemple pièces métal carrosserie).
-Le métal sorti est alors inutilisable car, il est écrouit au maximum. L'écrouissage
se caractérise par une augmentation de la limite d'élasticité et de la dureté.(écrasement et étirement) donc (pression-traction).Le métal n'est pas malléable ni emboutissable!.....
c-à-d :les grains du métal en sortie sont (écrasés et allongés) c'est un méta
dur et cassant.
- Le recuit ------Après laminage à chaud----------------------------------
-Pour rendre le métal propre au formage,(plus maléable, moins
cassant et emboutissable), il faut encore quelques étapes: Après laminage à froid
la bobine part au recuit afin de subir une température de .+/- 700°. Le recuit,
permet de détruire l'effet de l'écrouissage (laminage à froid) sert à rendre le métal propre au
formage, il confère au métal une taille de grain optimale pour son utilisation future (pliage, emboutissage),
-Le métal recuit est mou, très élastique, il n'est pas
encore prêt pour subir un emboutissage ou formage. (ex: les pièces de carrosseries.), il faut encore quelques étapes :
-Le recuit, permet de détruire l'effet de l'écrouissage(laminage à froid),
il à pour but de conférer au métal
une taille de grain optimale pour son utilisation future (pliage, emboutissage). Les bobines sont empilées verticalement
l'une sur l'autre, puis le tout est couvert avec une cloche, puis vient le four qui s'enfile par dessus. Ici, (au dessus) en rouge c'est une
cloche qui refroidit, les bobines sont à l'intérieure, et en haut de l'image, on voit
le four qui descend sur la cloche froide.A droite, les fours qui recouvrent les cloches.
- Le Skin pass - Finalise la qualité du métal et de son aspect de surface.
-Alors que le laminage à chaud a pour but de mettre en forme le
matériau, le laminage à froid permet de modifier les caractéristiques mécaniques du métal. De fait, l'écrouissage local (qui consiste en une
déformation plastique) augmente la zone de déformation élastique. De cette manière, la limite d'élasticité est repoussée, tout en gardant constante la
résistance à la rupture. Il transforme un produit laminé à chaud en bobine de métal extrêmement fine, soit moins de 3 millimètres en sortie.
Ici, le métal (bande) est très légèrement allongé.La bobine se déroule et la bande passe entre 2 cylindres avec
un très faible écrasement et une traction en sortie de +/- 2% pas plus.
l'épaisseur entrée: sortie, ne bouge que de 1 ou 2% .
C'est ici, que le métal trouve sa qualité d'emboutissage
et de surface, grâce à la rugosité des cylindres qui ont été grenaillés (bombarder de grenaille de limaille de fer) de plus ou moins gros calibre, la surface de la
bande et, alors ou brillante ou rugueuse à différents degrés.
-
Une fois la bobine skinpasée, elle partira, chez le client,
ou, elle
va sur une ligne d' inspection, les bobines sont misent à poids, soit on coupe le trop,
ou que l'on soude cette bobine a une suivante et que l'on coupe (le tout) au bon poids. DONC les bobines ont ou pas, de soudure.
-L'épaisseur de la bande est contrôlée automatiquement et contrôle visuel de sa surface.
ici: Bobines sortant du skin pass. La surface du métal
peut être granuleuse ou brillante suivant la commande.
- ici dessous: Aspect des Bobines, suivant leurs étapes-
1- Aspect avant décapage: (venant du laminage a chaud.)
2- Aspect sortie: Laminage a froid (5 cages)
3-
Sortie finisseur (Skin pass) (ici une sele cage)
---------------- Chez un client --(1990)---------------
-Les bobines de métal arrivent
pour être découper et embouties en
toutes sortes
de pièces. Voila le début de la construction de notre voiture. Certaines presses sont hautes comme un immeuble de 4 étages et parfois bâtis sur un sous sol de 4 étages!
(1990)
Ici à 5h 30. La bobine est coupée en feuilles pour subir un emboutissage plus ou moins profond suivant sont utilité.
..(expl aile de voitures, radiateurs chauffage, etc..)
-
Les feuilles arrivent à la presse d'emboutissage (à droite).
L’emboutissage mécanique est un procédé de formage de pièces qui nécessite des machines telle qu’une presse mécanique et un outillage adapté.
-Le principe est fondé sur la déformation plastique du matériau (en général un métal), déformation consistant en un allongement ou un retreint de la tôle pour obtenir la forme souhaitée.
-On distingue l’emboutissage à froid qui se pratique à température ambiante et l’emboutissage à chaud qui lui se pratique avec une pièce
chauffée à 800 °C environ pour de l’acier doux. L’emboutissage à froid est le mode opératoire le plus utilisé pour des productions de grandes ou de très
grandes quantités de pièces nécessitant simplement une action unilatérale puissante.
-L’emboutissage à froid peut être pratiqué avec une presse pneumatique (jusqu’à 6 tonnes), ou des presses
hydropneumatiques (jusqu’à 30 tonnes) mais pour des productions de grandes quantités, les presses mécaniques sont plus adaptées. Leur puissance de frappe
et leur rapidité d’exécution leur permettent d’atteindre une productivité bien supérieure à des presses pneumatiques et hydropneumatiques.
A 20h40, La golf finie est sur wagon. De nos jours les usines sont modernisés avec d'autres matériels comme des chaines de robots.-Quelques photos de fabrication Autos Récentes.
Ou: Acier Composition ici
le créateur de oocbo.com" revu 2022vr
24vr